LOG MAX
We design and manufacture high-tech harvester heads for forestry machinery.
RELIABLE
Our harvester heads are known for their reliability, the basis for this is the heads' well-thought-out design and our patented AFC system.
GOOD LENGTH MEASUREMENT
Our reliable and accurate length measurement contributes to more efficient forest harvesting and better resource utilization.
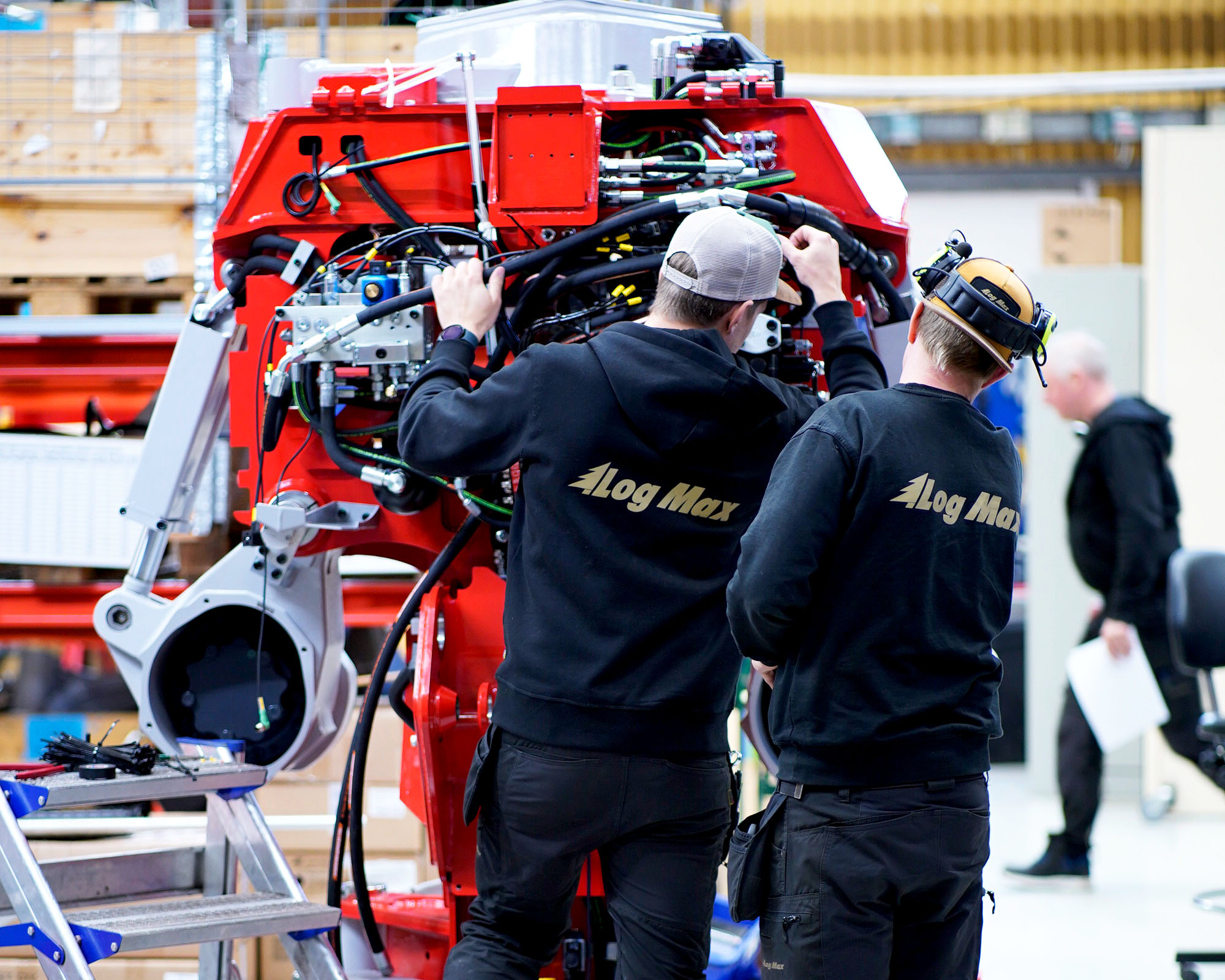
WORK WITH US
At Log Max, we have close to 100 employees - here you can see our available vacancies.
Learn more
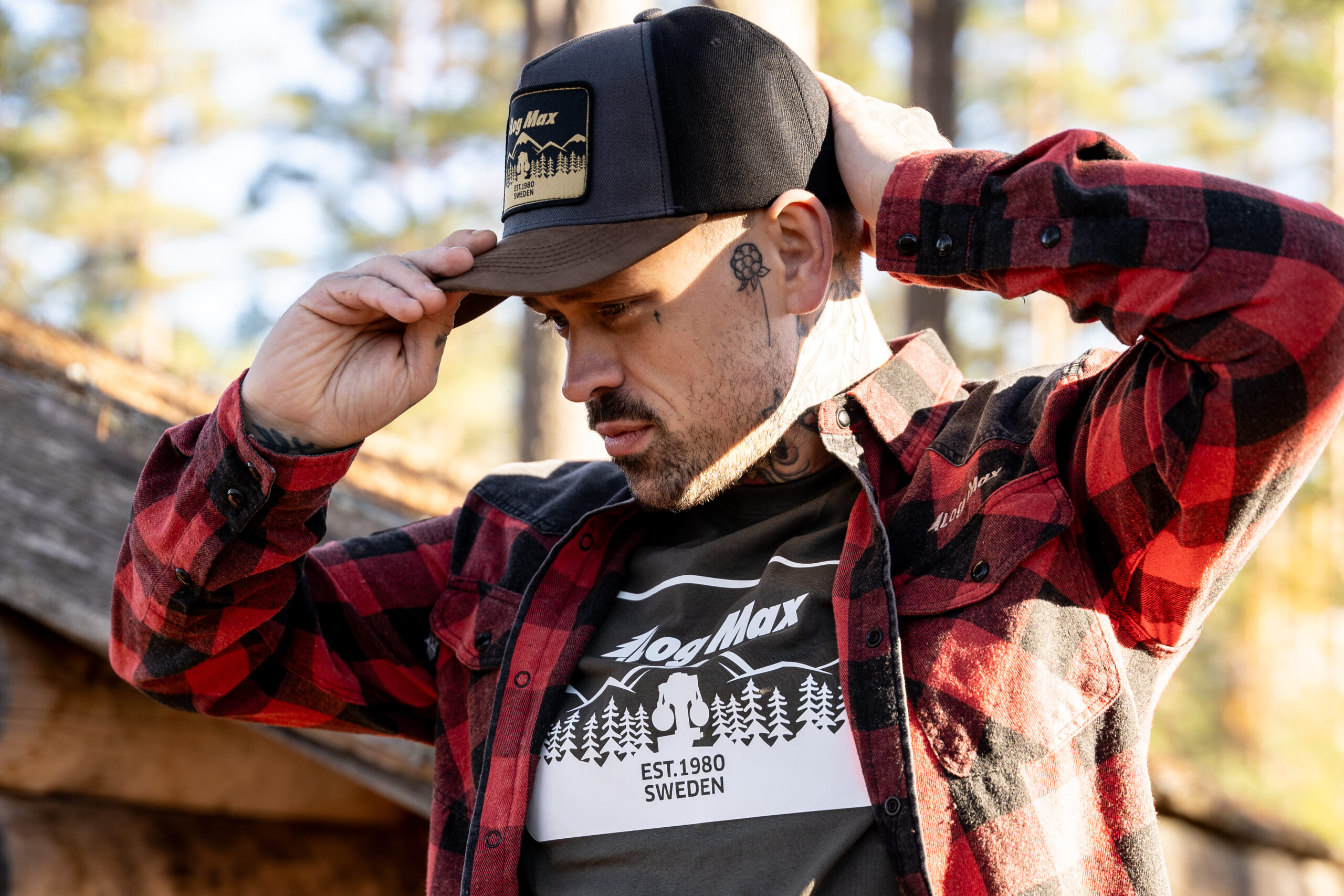
Clothing collection
Explore our clothing collection - here you will find stylish and durable clothes.
Learn more

LOG MAX HISTORY
Log Max was founded 45 years ago, here you can read more about our history.
Learn more